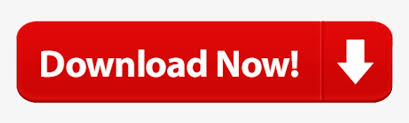
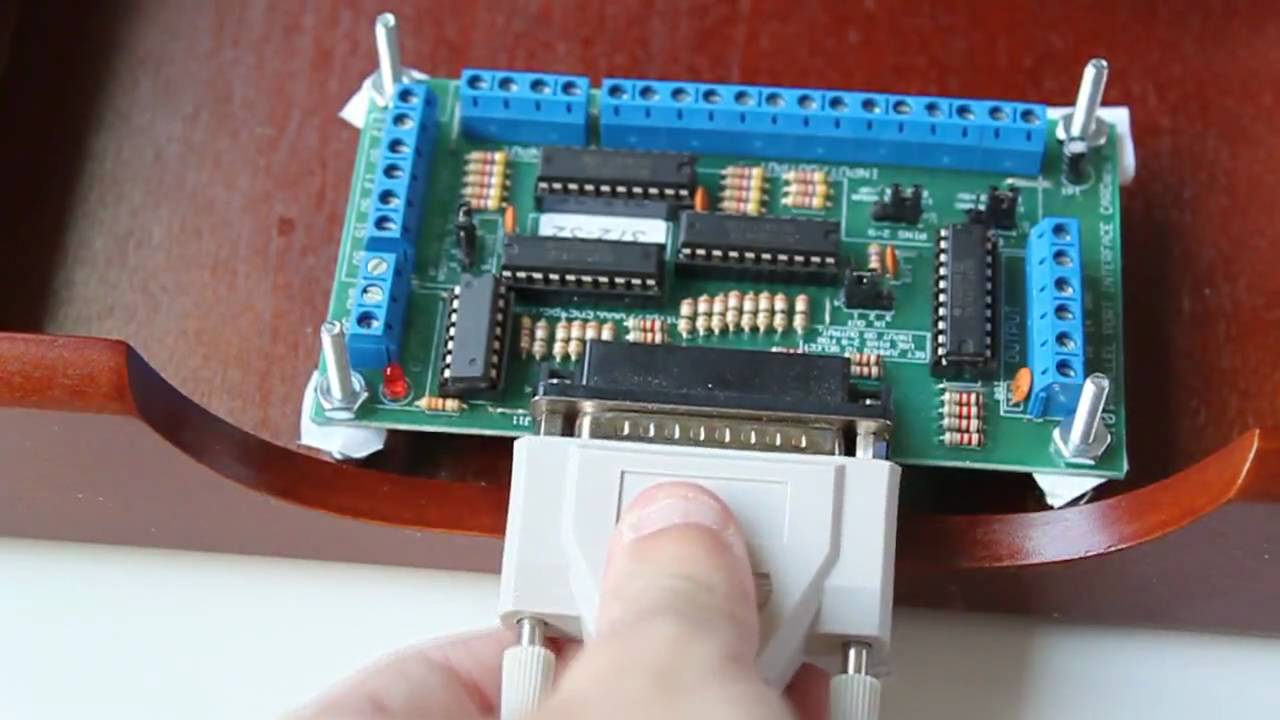
- #DIY PARALLEL PORT CNC CONTROLLER HOW TO#
- #DIY PARALLEL PORT CNC CONTROLLER DRIVER#
- #DIY PARALLEL PORT CNC CONTROLLER PC#
I have a PC> parallel port> controller card> drivers> stepper motors. I also suggest you use Protoneer and the assembly of the Laser Plotter performed in the first video on this subject.ġ - Mach3 = Example of a router that I have:
#DIY PARALLEL PORT CNC CONTROLLER PC#
The automation of these machines requires CNC control, so you can do many things by understanding this system.Ĭonsidering the image above, my personal suggestion is that you use Raspberry instead of the PC with Arduino Uno. These are all the same because the origin is the same. It is important to remember that when I talk about CNC (Computer Numeric Control), in addition to the laser plotter, I'm also talking about a router, a milling machine, and a CNC lathe. The feature is very efficient for the automation of CNCs.
#DIY PARALLEL PORT CNC CONTROLLER DRIVER#
It has a 40W GPIO connector and supports the special auto configuration system, which allows for automatic configuration of the GPIO and driver configuration. Today, we are going to talk about the HAT (Hardware attached at the top), which is a rectangular plate that has four mounting holes in the corners that align with the Raspberry Pi mounting holes. This gives continuity to the subject covered last week entitled, “Plotter and Laser with Raspberry Pi CNC HAT,” where we set up a laser plotter with an XY table. We’ll mount this HAT and configure the GRBL. We will prepare a Raspberry Pi 3 with the RPI CNC V4 image using HAT version 2.58.
#DIY PARALLEL PORT CNC CONTROLLER HOW TO#
Then tick on Run MacroPump in Mach3 General Config.Īfter that, restart Mach3 to enjoy the result.Today we’ll learn how to configure CNC with Raspberry Pi. Save, copy and paste it into C:\Mach3\macros\Mach3Mill If GetOemDRO(828)=0.01 and GetOemLED(15) Then If GetOemDRO(828)=0.1 And GetOemLED(15) ThenĭoOEMButton (235) DoOEMButton (234) DoOEMButton (238) If GetOemDRO(828)=1 and GetOemLED(15) Then When the button which was set 301 is pressed (here is Trigger #11), script on M300 will be run. This requires Mach3 run macro M299 at startup. Then add M299 to Initialization String in Mach3 General Config.
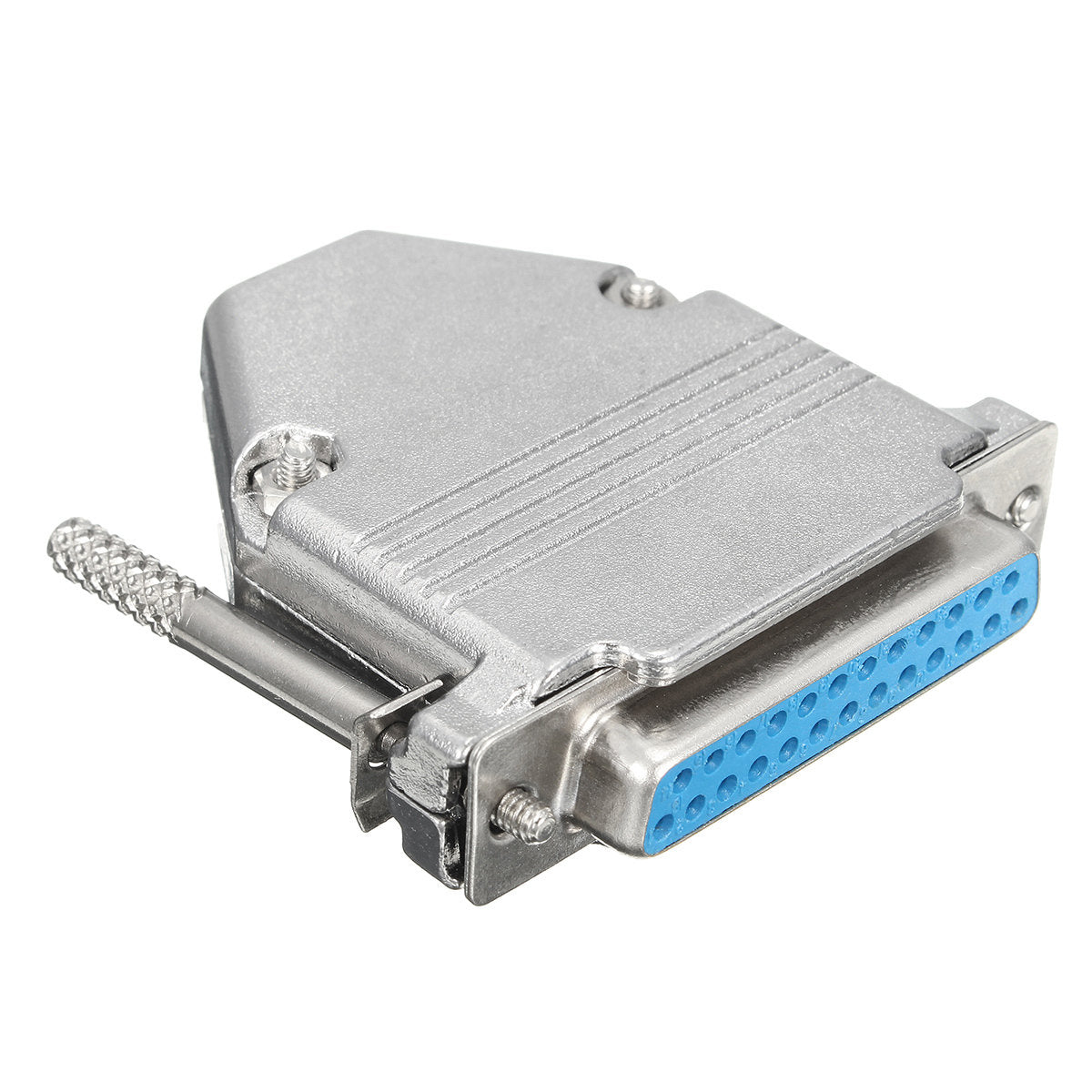

Save, copy and paste both into C:\Mach3\macros\Mach3Mill If IsActive (OEMTRIG11) And getoemled (63) Then If IsActive (OEMTRIG11) And getoemled (62) Then If IsActive (OEMTRIG11) And getoemled (61) Then If IsActive (OEMTRIG11) And getoemled (60) Then If IsActive (OEMTRIG11) And getoemled (59) Then I used Port #1 for connecting to the break-out board and Port #2 for MPG.Ĭreate 2. I bought one more PCI-express to LPT card because my computer had only one LPT port.Īfter installing driver, copy the address in Device Manager then paste it into Mach3 Port Setup. 1 red led to indicate that MPG being ONīeside, E-stop and the big red button go to the break-out board, irrelevant to LPT port.īecause of having no time, a plastic box seemed to be not bad for me.3 blue leds turn on interchangeably by changing the jog step: 1 0.1 0.01.one button to show virtual MPG on the PC screen.one 5 positions switch to select 5 axes.It took me a while to complete the schematic.

I used a USB port to get 5V directly from my computer, not need external power.Īfter trying several times, I realised that 13 pins (included 8 yellow pins and 5 blue pins) can be used as input 5 red pins can be used as output 8 green pins are ground. My 5 axes milling machine did not have MPG pendant handwheel, so I wanted to create one to use it conveniently.įirst, I tried with some buttons and a mouse-wheel encoder to know how does LPT port work.
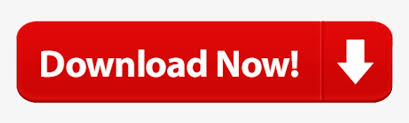